The term ASEPTIC PACKAGING essentially means filling pre-sterilised packaging with pre-sterilised product in a hygienic environment. That doesn’t sound terribly exciting at first hearing, but turning that concept into reliable technology has had profound consequences for the food and drinks industries. ASEPTIC PACKAGING offers the possibility of presenting highly perishable food in a convenient form that remains in good condition for at least six months without refrigeration. Of course, traditional canning technology can do that too, and using a much simpler procedure. So what is so special about aseptic packaging?
The key feature of ASEPTIC PACKAGING is that the sterilisation of the product and the packaging are separate processes. This means that the sterilisation of the product can be optimised to protect its taste, colour and nutritional content, usually by heating rapidly in a heat exchanger, or by direct steam injection, to high temperatures (140 - 150 oC) for just a few seconds. This produces a safe heat process, but has a much less detrimental effect on the quality of the product. This gives aseptic packaging the potential to make a whole new range of foods available in a shelf-stable and convenient format.
That was exactly what Sweden’s TETRA PAK Company recognised when it launched the world’s first aseptic food package in 1961 and it's still the biggest market success today with more than 20 bio € turnover every year!
Here some innovative ASEPTIC FLEXIBLE PACKAGING solutions recently launched on the market which seems to cover well existing consumers needs.
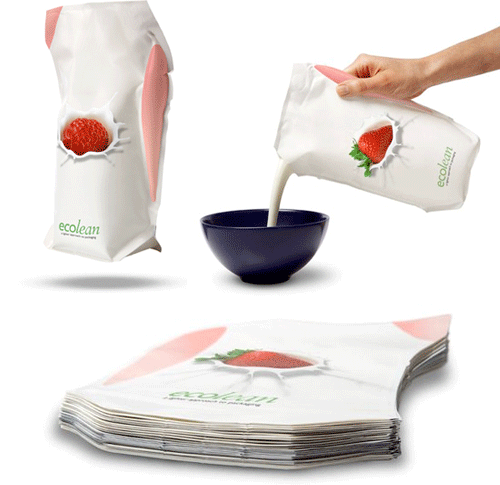
www.ecolean.com
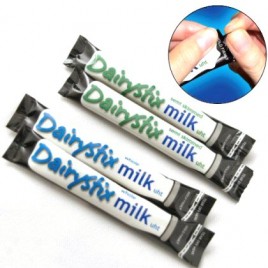
http://www.dairystix.com/
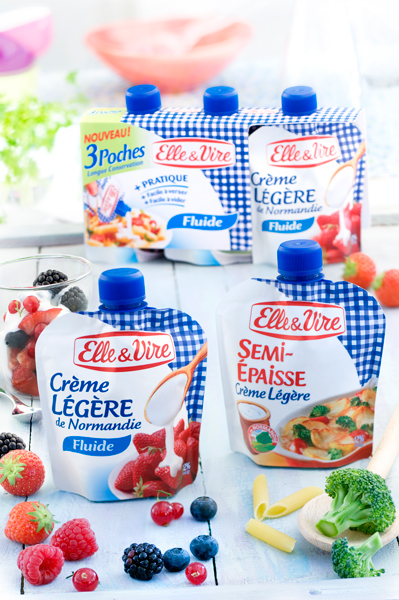
[ add comment ] ( 188 views ) | permalink |





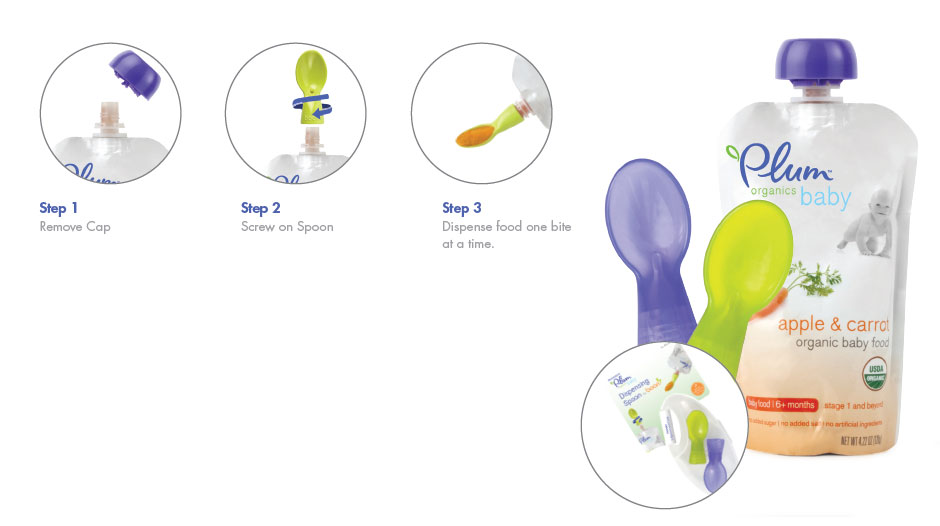
A STAND-UP POUCH (SUP) capped by a large reclosable and tamper-evident closure is a packaging format lunched successfully by The Nest Collective company in the States.
This baby and kid-focused consumer products company brings a whole new level of portability and convenience to its category by using a new
spouted pouch for packaging their Plum Organics line.
The company belives that this new pouch format is far superior to the glass jar, which is still the market standard pack in use world-wide.
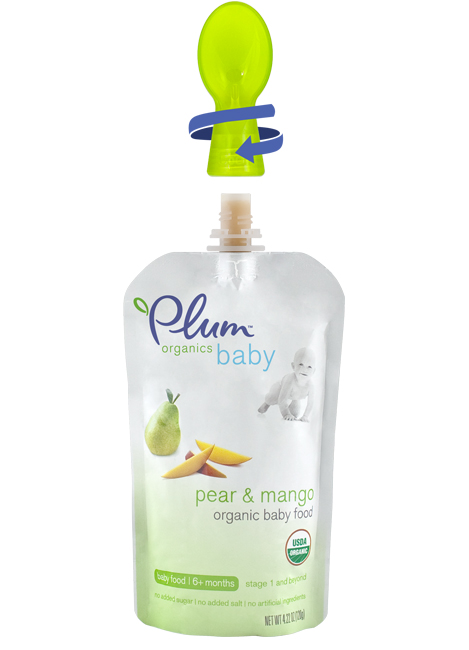
TWIST-ON SPOON. The lastest enhancement added to the Plum Organics line a twist-on spoon that delivers one-piece squeeze and feed convenience.
SIMPLY GREAT!!!!!
[ add comment ] ( 19 views ) | permalink | related link |





.jpg)
Shelf-Ready Packaging (SRP)
This term is used to describe shelf units that demonstrate the following characteristics:
• Fulfilment of special handling and design properties in addition to logistical requirements
• Broadest possible advance preparation for sale at POS
Attractively designed, shelf ready packaging represents a strong dose of efficiency for retailers and manufacturers and a major aid to sell-through.
Requirements for Shelf-Ready Packaging
Retailers look for packaging that is simple and easy to open without a knife, demonstrates a high degree of shelf impact and is easy to dispose of once empty.
I. Right size
Optimised packaging format in terms of logistics, module dimensions and unit count for most effective sell-through.
II. Simple product identification and visibility
The information on the shelf-ready packaging must allow the POS staff to identify where the product belongs quickly and easily.
III. Simple to open
The packaging must be easy to open at the POS yet be robust enough to survive intact the entire logistics chain from manufacturer to retailer.
IV. Simple placement and restocking
Retailers look for shelf packaging that makes it possible to stock and restock the entire shipment of goods onto the shelves in one step.
V. Simple purchasing / quick orientation
Shelf placement and packaging design help consumers find the goods they desire more quickly.
VI. Simple disposal / return
Lowest possible material consumption for the shelf packaging. Ideally with use of durable transport containers.
Studies by the ECR Europe have shown that many common causes for out-of-stock rates at the POS are related to the last 50 meters:
• Inefficient shelf stocking
• Poor identification of goods
• Difficult-to-open external cartons
Shelf Ready Packaging (SRP) is a suitable solution for those problems.
SRP evolved from the basic requirements for disposable transit packaging as recommended by GS1 Germany:
• Protecting goods against damages
• Modularity in the logistics chain
• Marketing and sales-oriented requirements
• Consideration of product and manufacturer liability issues
• Process considerations for transport, warehousing and picking
• Adherence to packaging ordinances
• Consideration of cost aspects
SRP packaging also fulfils other so-called functional requirements. SRP represents a more effective application of resources than the exclusive use of disposable transit packaging:
• Lower out-of-stock rates at the POS
• Attractive product presentation
• Easier purchasing process for customers
• Increased planned and spontaneous purchases
• Increase in revenues
A video can better explain this new market request!!
http://www.youtube.com/watch?v=7UgqBcKaYyk
[ add comment ] ( 119 views ) | permalink |





From Douglas G. Davidoff
Founder & CEO, the Imagine companies
How easily can you quantify the differences between your products and services from those of your competitors? How easily can your clients or prospects make those same distinctions? How can you continuously differentiate your company when market forces are constantly commoditizing your business? Think about that question for a moment. It is the biggest challenge facing businesses of all sizes in the 21st century.
Commoditization is the evolutionary process that reduces all products and services to their lowest common denominator. The Commoditization Trap is the situation businesses find themselves in when their focus is mainly on the product or service they offer instead of a quantifiable difference between their product and their competitor’s.
Imagine Consulting has asked over 2,000 business owners and salespeople “Why should people buy from you instead of your competitors?” Here is what many answered:
- We give better service.
- Our clients get better results with us.
- We know what we’re doing better than our competition does.
- Our products and service are better.
These answers may sound familiar. But as nice as they sound, and even as true as they may be, these answers are all indicative of a we are better value proposition. Distinguishing your company in such a manner puts you in The Commoditization Trap™. These answers do not differentiate you. No one is out there saying: “We’re not as good.” Even companies for which price is the primary selling point insist that their products are just as good.
The Commoditization Trap, ensnaring businesses, impacts businesses in ways not readily apparent to them. Unaware of the causes of commoditization, businesses often unnecessarily expend valuable resources. Addressing the symptoms of commoditization, rather than focusing on their origin, businesses look internally to solve the problem. This actually propels them deeper into the trap. Businesses invest in new product development. They change their marketing plans. They change their advertising. They reprint their brochures. They change the sales process by eliminating salespeople if they have a sales force or hiring salespeople if they do not have a sales force. In an attempt to get out of the trap, businesses do all of this under the mantra of “ giving added value” to their customers. The problem, however, is that businesses fail to ask themselves if any of these changes actually add value.
CONCLUSIONS
The tighter "The Commoditization Trap" is on a company or an industry, the more that company or industry must look outside – to its customers, clients and prospects to find, and, more importantly, understand the unique problems that face them. Companies must stop being “solution” specialists and become “problem” specialists. If you want to avoid or escape "The Commoditization Trap" you must find ways to add value (something people are willing to pay for) before the product or service becomes an issue.
From a packaging development specialist point of view, like we are, the COMMODITIZATION TRAP is not only a "danger" , but a reality caused and accellerated by:
- the increase of Food safety issues, norms and requests of controls
- the standardization of the materials imposed by local pubblic laws to facilitate the waste management.
- the buying activity for facilitate the e-auctions
- the research of the max efficiency possible on existing process
- the necessity of intensive capital for the development of innovative more sustinable materials, process and solutions.
SO PLEASE ASK US TO SOLVE YOUR PROBLEMS INSTEAD TO LOOK FOR INNOVATIVE SOLUTIONS!!!
https://www.youtube.com/watch?v=Hssd84U2470
A good example will follow!!
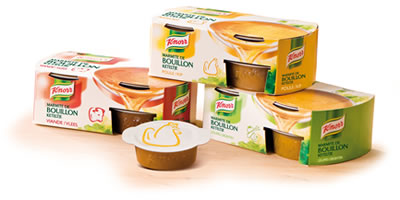
[ add comment ] ( 17 views ) | permalink |





I am not big a supporter of the so called "Sustainability packaging solutions", because I find them more a marketing tool than a real development that can be used in a consistent manner by the industry to pack products more ecologically!!
Sometimes you will find some intelligent industrial solutions, like this one, which is good to be mentioned!
Innovia Films has recently launched in USA a new high barrier NatureFlex™ range of renewable and compostable cellulose-based packaging films for the North American market. The new films, NatureFlex™ NKR and NKA, manufactured in Tecumseh, KS, provide the highest moisture barriers of any transparent bio-film on the market.
NatureFlex contains over 90% renewable content as measured by ASTM 6866 and is produced from wood pulp sourced from managed plantations that either have or are actively working towards Forest Stewardship Council (FSC) certification or equivalent. The product is also compostable and meets the requirements of ASTM D6400, composting within six weeks.
Both these films provide an excellent barrier to gases and aroma, a good barrier to moisture and have a wide heat-seal range. They also offer advantages for packing and converting such as inherent deadfold and anti-static properties, high gloss and they are resistant to grease and oil. NKA and NKR films are ideal for packing moisture-sensitive products such as coffee, cookies, condiments, chips, bakery, and cosmetics. Types of pack construction the films could be used in include—twist wrap, overwrap, pouches, sachets, lamination with other bio-films, HFFS flow wrap, and VFFS bags. For more, visit www.innoviafilms.com.
I hope that some companies will take note of it!
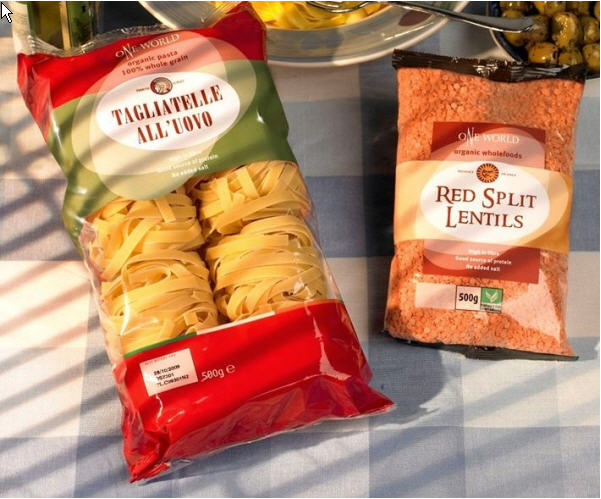
[ add comment ] ( 16 views ) | permalink |




